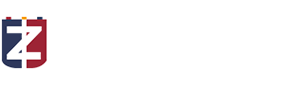
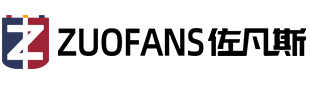
Quality guarantee
The company has a complete set of technological processes such as smelting, electroslag remelting, forging, rolling, shearing, machining, heat treatment and surface treatment. And can realize further utilization of returned material and leftover material. Zhejiang Jingrui will gradually phase out its own smelting capacity in the future, purchase slabs from large state-owned enterprises for back-end processing, and extend the industrial chain to back-end deep processing products.
1. SMELTING
Our high-quality tools go through an induction furnace for pre-melting and alloy adjustment and slag removal. The relatively small induction furnace type ensures greater flexibility in our process, allowing Jingrui to smelt small batches, multiple varieties, and customized special steel grades for customers.
In addition, the advantage of induction furnace is to minimize the burning loss of alloying elements during the smelting process of tool and die, and the alloy yield is high; the chemical composition control is accurate and stable; the utilization rate of return material is high, and the cost is effectively reduced.
During the smelting process, we analyze the chemical composition of the samples several times with a spectrometer, and fine-tune in the subsequent process to ensure accurate alloy composition.
2. LF+VD REFINING OUTSIDE THE FURNACE
Through our subsequent out-of-furnace technical processing, the quality of our tooling materials can reach a higher level.
We adopt LF+VD out-of-furnace refining process to effectively remove N, O and other gas content in molten steel and improve the purity, so as to meet the increasingly complex market demand and domestic high-quality tool and die steel standards.
3. ESR ELECTROSLAG REMELTING
High quality electroslag ingots can be produced by our atmosphere protected electroslag remelting equipment. Improve the crystal structure of the ingot; reduce the non-metallic impurities and inclusions in the steel; control the atmosphere in the furnace to prevent the content of H, N, and O in the steel from increasing. Meet customer requirements for high purity materials.
4. FORGING/ROLLING BILLET
Through the forging/rolling blanking process, the electroslag ingot is hot processed into semi-finished slabs suitable for rolling; or forged blanks of different specifications are made as finished flat steel products. Through our 8T air hammer or 1700 rolling mill, the ledeburite and banded carbides in the high-speed steel ingot can be fully broken to obtain fine and dispersed microstructure. A carefully controlled annealing process ensures optimum forging structure and machinability.
5. ROLLING
Plates of custom-made dimensions are produced in Jingrui's unique 1400-1250 hot rolling production line and cold rolling workshop, and we pay special attention to customer requirements. To guarantee high quality, all sheets are produced by cross-rolling. The sheets in the delivery state all pass our flattening process, vacuum annealing process, surface treatment process, etc. Ultrasonic equipment is used to inspect the thickness tolerance of the plates, and each plate is inspected for surface defects to ensure the quality and supply stability of the ex-factory plates.
6. MACHINING
Through subsequent straightening and finishing, laser cutting, stamping forming, grinding, milling, CNC machining center and other machining processes. Deep processing derivatives of plates and flat steels can be obtained: circular saw blades, fine plates, planing knives, turning knives, etc. At the same time, it can meet the customized needs of customers, and customize the finished tools according to the drawing requirements.
products